How Keyless Drill Chucks Improve Workflow Efficiency in Manufacturing
- zhejiangbried
- Oct 29, 2024
- 3 min read
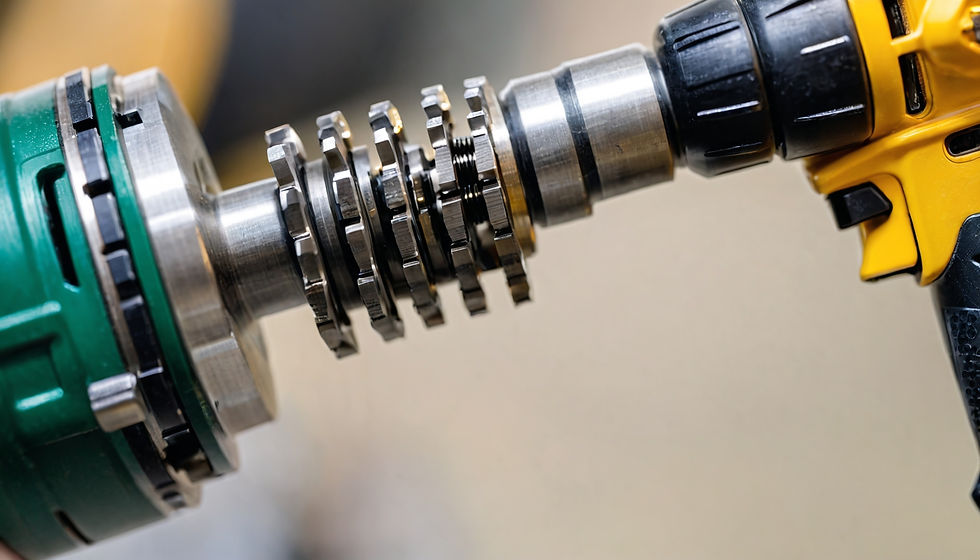
In manufacturing, every second counts. Whether on assembly lines or in specialized machinery work, productivity is key to meeting deadlines, reducing costs, and maintaining a high-quality standard. While often overlooked, a simple upgrade like using a keyless drill chuck can have a considerable impact on workflow efficiency. Here’s how keyless drill chucks are helping manufacturers optimize their operations and streamline processes.
Fast, Tool-Free Bit Changes
One of the most significant advantages of keyless drill chucks in a manufacturing setting is the ability to change bits quickly without needing a separate tool. Unlike traditional chucks that require a chuck key to tighten or loosen, keyless chucks allow workers to twist the chuck by hand. This tool-free design means operators can switch between drill bits in seconds, reducing time wasted on finding or misplacing chuck keys.
In fast-paced manufacturing lines where workers may change bits multiple times per shift, this quick-change capability can save valuable minutes, allowing tasks to move along smoothly. With faster bit changes, manufacturing plants see reduced bottlenecks, resulting in improved overall productivity.
Enhanced Grip and Consistent Stability
A secure grip is critical when performing precise work, particularly in environments where high torque is involved. Keyless drill chucks are engineered to grip the bit tightly, often incorporating self-tightening mechanisms that ensure a secure hold. As the drill spins, the chuck tightens automatically around the bit, preventing it from loosening or slipping.
This stability means there’s less risk of drill bits wobbling or coming loose during high-intensity operations. For manufacturers, this consistent performance is crucial to avoid rework, ensure accuracy, and maintain a high-quality product output. Keyless chucks also reduce the chances of damaging parts or tools, which lowers maintenance needs and prolongs equipment life.
Improved Safety and Reduced Downtime
Keyless drill chucks make it easier for workers to handle and operate drills safely. The twist-to-lock design allows users to feel when the bit is secure, helping prevent loose bits that could lead to injuries or damaged workpieces. With less need to fumble with small chuck keys, workers can avoid distractions and stay focused on their tasks.
Reduced safety incidents contribute to smoother, uninterrupted operations. Additionally, keyless chucks generally have low maintenance, which means less downtime for recalibration or repair. In manufacturing settings where uptime is essential, these safety and reliability improvements contribute directly to workflow efficiency.
Versatility in Multi-Task Environments
In manufacturing, the ability to adapt quickly to different tasks is invaluable. Keyless drill chucks are compatible with a range of drill types and sizes, making them ideal for environments where operators frequently switch between applications. From drilling and fastening to grinding and sanding, keyless chucks allow workers to swap attachments effortlessly.
For example, on an automotive assembly line, workers might use the same drill for tasks requiring different bit types or sizes. With a keyless drill chuck, they can seamlessly transition between tasks without changing tools, reducing idle time and enhancing the flexibility of the work process.
Ergonomic Benefits for Workers
An often-overlooked benefit of keyless drill chucks is their ergonomic design. Traditional chucks can lead to hand strain from using chuck keys or over-tightening bits. In contrast, keyless chucks require minimal twisting effort, reducing the strain on workers’ hands and wrists.
This ergonomic advantage is especially valuable in manufacturing settings where workers may use power tools for long shifts. By decreasing the risk of repetitive strain injuries, keyless chucks contribute to a safer, more comfortable workplace. Ergonomically designed tools can improve employee satisfaction, reduce turnover, and minimize time off due to injuries—all of which indirectly enhance efficiency.
Ideal for Battery-Powered Tools
With the rise of battery-powered tools, keyless drill chucks have become even more relevant in manufacturing. The quick-change design of a keyless chuck allows workers to swap bits without drawing excessive power, which helps preserve battery life and reduces the need for frequent recharges.
This feature is especially useful in manufacturing settings where workers rely on cordless tools for flexibility and convenience. Extended battery life translates to fewer interruptions, allowing employees to work continuously and keep up with production demands.
Why Keyless Drill Chucks Are the Right Choice for Modern Manufacturing
When it comes to choosing tools that enhance productivity without compromising safety or quality, keyless drill chucks are an excellent investment. From fast bit changes and improved grip to ergonomic design and compatibility with battery-powered tools, these chucks help streamline manufacturing processes and reduce operational costs.
For manufacturers looking to upgrade their toolsets, working with an exporter of keyless drill chucks ensures access to high-quality, durable chucks that meet their specific workflow needs. By embracing this efficient tool, manufacturing facilities can gain a competitive edge, reduce downtime, and build a more productive work environment.
In a world where efficiency is everything, keyless drill chucks offer a simple yet effective solution to improve workflow, save time, and increase the quality of work in manufacturing settings. As more facilities adopt these advanced chucks, they are likely to become a standard tool in the industry, driving continuous improvements in productivity and performance.
Comments